CO₂ arc welding different droplet transfer form
- Share
- publisher
- sandy
- Issue Time
- Sep 26,2016
Summary
The gas metal arc welding (GMAW) process uses four basic modes to transfer metal from the electrode to the workpiece. Each mode of transfer depends on the welding process, the welding power supply, and the consumable, and each has its own distinct characteristics and applications.
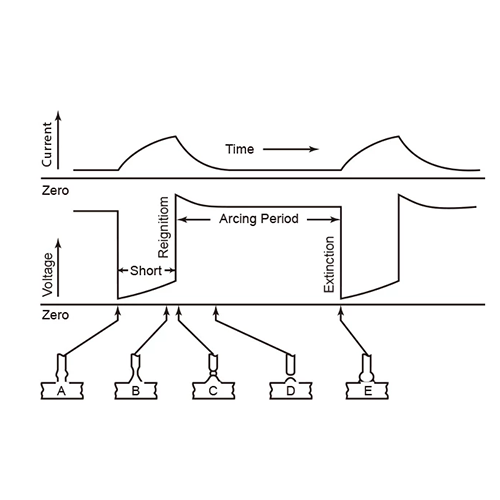
The gas metal arc welding (GMAW) process uses four basic modes to transfer metal from the electrode to the workpiece. Each mode of transfer depends on the welding process, the welding power supply, and the consumable, and each has its own distinct characteristics and applications.
Several variables dictate the type of transfer you use, including the amount and type of welding current, the electrode chemistry, electrode surface, electrode diameter, shielding gas, and the contact tip-to-work distance. Transfer mode also affects your choice of filler metal used.
Which mode is right for you? Choosing wisely can greatly affect your efficiencies and productivity.
Short-circuit Transfer
This mode of transfer generally calls for smaller-diameter electrodes, such as 0.023, 0.030, 0.035, 0.040, and 0.045 in. The welding current must be sufficient to melt the electrode, but if it is excessive, it can cause a violent separation of the shorted electrode, leading to excessive spatter. Using adjustable slope and inductance controls can enhance the transfer to minimize spatter and promote a flatter weld profile. Slope adjustment limits the short-circuit amperage, while inductance adjustments control the time it takes to reach maximum amperage. Proper adjustment of these two factors can produce excellent bead appearance and is essential for short-circuit transfer with stainless steel electrodes.
The most common shielding gas for the short-circuit transfer mode for carbon steel electrodes is 75 percent argon/25 percent CO₂. Numerous three-part shielding gas mixes are also available for carbon steel and stainless steel for this mode of transfer.
Oscillograms and Sketches of ShortCircuiting Transfer
Globular Transfer
Globular transfer means the weld metal transfers across the arc in large droplets, usually larger than the diameter of the electrode being used. This mode of transfer generally is used on carbon steel only and uses 100 percent CO₂ shielding gas. The method typically is used to weld in the flat and horizontal positions because the droplet size is large and would be more difficult to control if used in the vertical and overhead positions compared to the short-circuit arc transfer. This mode generates the most spatter; however, when higher currents are used with CO₂ shielding and a buried arc, spatter can be greatly reduced. You must use caution with a buried arc because this can result in excessive reinforcement if travel speed isn't controlled
Spray Transfer Mode
Spray transfer is named for the spray of tiny molten droplets across the arc, similar to spray coming out of a garden hose when the opening is restricted. Spray transfer usually is smaller than the diameter of the wire and uses relatively high voltage and wire feed speeds or amperage. Unlike short-circuit transfer, once the arc is established, it is on at all times. This method produces very little spatter and is most often used on thick metals in the flat and horizontal positions.
Pulse-Spray Transfer
The pulse-spray transfer mode, the power supply cycles between a high spray transfer current and a low background current. This allows for supercooling of the weld pool during the background cycle, making it slightly different than a true spray transfer. Ideally, in each cycle one droplet transfers from the electrode to the weld pool. Because of the low background current, this mode of transfer can be used to weld out of position on thick sections with higher energy than the short-circuit transfer, thus producing a higher average current and improved side-wall fusion. Additionally, it can be used to lower heat input and reduce distortion when high travel speeds are not needed or cannot be achieved because of equipment or throughput limitations.
Generally, the same shielding gases used for spray transfer are also used for pulsed-spray mode