Different Types of Welding
- Share
- Issue Time
- Apr 5,2017
Summary
Stick Welding (SMAW or Shielded Metal Arc Welding)
MIG Welding (Metal Inert Gas, also known as GMAW or Gas Metal Arc Welding)
Flux Cored Arc Welding (FCAW)
TIG Welding (Tungsten Inert Gas, also known as GTAW or Gas Tungsten Arc welding)
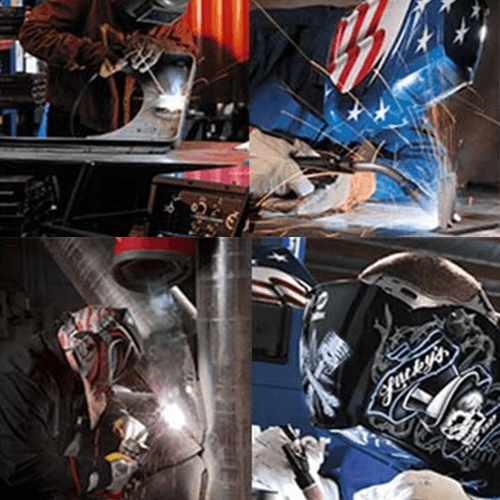
There are more than thirty different types of welding, from simple oxy-fuel (using a flame) welding to high-tech processes such as laser beam welding. The four most commonly used welding is MIG, TIG, Stick and Flux- Cored arc welding. This article will explain the difference between them.
Electric welding is the joining of metal using an electrical arc and a filler metal stick electrode or wire. Welding is done by creating an arc between the base metal (the metal being welded) and the filler metal. The arc melts the base metal and filler metal, combining them into one material to join the base metals. The filler metal is consumed in the process.
Stick Welding (SMAW or Shielded Metal Arc Welding)
Stick welding (also called SMAW or Shielded Metal Arc Welding) is the process of melting and joining metals by heating them with an arc between a covered metal electrode (rod/stick) and the workpiece. Shielding gas is obtained from the electrode outer coating (called flux).
For more details about TOPWELL Stick Welding
Typical Uses: Steel Erection, Heavy equipment repair, Construction, Pipeline Welding
Advantages | Disadvantages |
Low cost equipment, Portability | Lower consumable efficiency (waste is produced) |
Welds steel, stainless steel, cast iron, hard surfacing, and aluminum | Difficult to use on thin materials |
No need for shielding gas (can be used outside during rain or wind) | High operator skill required |
Works on dirty or rusty metal | Tends to have more spatter than other processes |
MIG Welding (Metal Inert Gas, also known as GMAW or Gas Metal Arc Welding)
MIG (Metal Inert Gas) Welding (also called GMAW or Gas Metal Arc Welding) joins metals by heating them with an arc between a continuously fed wire (filler metal electrode) and the workpiece. The molten weld metal is protected from oxides and nitrides in the atmosphere by an externally supplied shielding gas. The GMAW process can be used to weld a wide range of alloys including carbon steel, stainless steel, magnesium, nickel, copper, silicon bronze and aluminum.
The type of shielding gas depends on the type of wire. For mild steel wire, the gas is C25 (that is, 75% Argon and 25% CO2) or CO2. For aluminum wire, the gas is Argon. For stainless steel wire, the gas is called "tri-mix" (a mixture of Argon, CO2 and helium).
For more details about TOPWELL MIG Welding
Typical Uses: Small to large manufacturing, Auto Body, Fabrication
Advantages | Disadvantages |
Higher Electrode Efficiency (Less Waste) | Need external shielding gas |
Lower Heat Inputs | Limited positions (no vertical or overhead) |
Minimal weld clean u | High cost equipment |
Reduced Welding Fumes | Cannot weld thick materials |
Easiest to learn | Material must be free of rust and dirt |
Flux Cored Arc Welding (FCAW)
Flux-cored Arc Welding is a welding process similar to GMAW, in that it uses a continuously fed electrode, but uses a tubular wire filled with flux instead of a solid wire. There are two types of flux-cored wire, self-shielded and dual shield. Self-shielded is used without the aid of an external gas shield and uses the flux to shield the molten weld puddle. Dual shield uses the flux and an external shielding gas to protect the molten weld puddle. Typical shielding gases are carbon dioxide and argon/carbon dioxide mixes. Self-shielded wires are optimal for outdoor use, even in windy situations. Both wires produce a slag covering on the finished weld.
Typical Uses: Thick materials, Steel Erection, Heavy Equipment construction or repair
Advantages | Disadvantages |
Higher Electrode Efficiency (Less Waste) | Creates slag |
Lower Heat Inputs | Not recommended for thin materials |
Minimal weld clean u | A lot of smoke is generated |
Reduced Welding Fumes | High cost equipment |
No need for external shielding gas |
|
TIG Welding (Tungsten Inert Gas, also known as GTAW or Gas Tungsten Arc welding)
Like the GMAW process, the molten weld puddle needs to be shielded by an external gas supply.
TIG Welding (also called GTAW or Gas Tungsten Arc Welding) is a welding process that uses a non-consumable tungsten electrode to heat the base metal and to create a molten weld puddle. The tungsten electrode, unlike a stick electrode, does not become part of the completed weld. An external filler rod can be added into the molten puddle to create the weld bead and increase mechanical properties. Like the GMAW process, argon inert gas or inert gas mixtures are used for shielding. Argon/helium mixtures can be used on heavy aluminum. GTAW can be used to weld most alloys.
For more details about TOPWELL TIG Welding
Typical Uses: Aerospace welding, piping systems, motorcycles or bikes
Advantages | Disadvantages |
Clean, high quality welds | High operator skill required |
Ability to weld very thin materials | High cost equipments |
Wide range of alloys can be welded | Lower deposition rates |
Spatter free welds | Need external shielding gas |
Highly aesthetic weld beads | Material must be free of rust and dirt |
Follow TOPWELL on Facebook.....
![]() | ![]() | ![]() | ![]() | ![]() | ![]() |