Welding Tips-MIG Welding
- Share
- Issue Time
- Oct 9,2019
Summary
These welding tips are meant to be helpful hints. See your equipment Owner’s Manual for all safety and operational information.
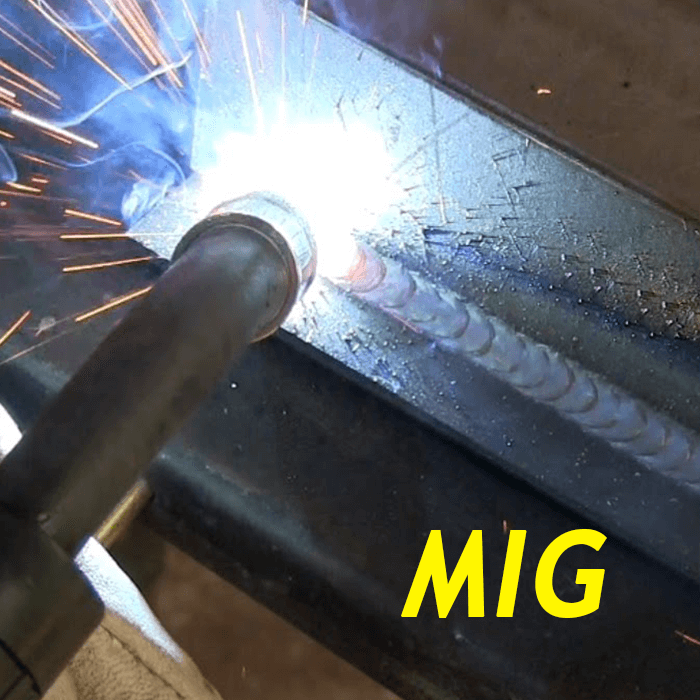
1.Keep a 1/4-3/8 in stickout (electrode extending from the tip of the contact tube.)
2. For thin metals, use a smaller diameter wire. For thicker metal use a larger wire and a larger machine. See machine recommendations for welding capacity.
3. Use the correct wire type for the base metal being welded. Use stainless steel wires for stainless steel, aluminum wires for aluminum, and steel wires for steel.
4. Use the proper shielding gas. CO2 is good for penetrating welds on steel, but may be too hot for thin metal. Use 75% Argon/25% CO2 for thinner steels. Use only Argon for aluminum. You can use a triple-mix for stainless steels (Helium + Argon + CO2).
5. For steel, there are two common wire types. Use an AWS classification ER70S-3 for all purpose, economical welding. Use ER70S-6 wire when more deoxidizers are needed for welding on dirty or rusty steel.
6. For best control of your weld bead, keep the wire directed at the leading edge of the weld pool.
7. When welding out of position (vertical, horizontal, or overhead welding), keep the weld pool small for best weld bead control, and use the smallest wire diameter size you can.
8. Be sure to match your contact tube, gun liner, and drive rolls to the wire size you are using.
9. Clean the gun liner and drive rolls occasionally, and keep the gun nozzle clean of spatter. Replace the contact tip if blocked or feeding poorly.
10. Keep the gun straight as possible when welding, to avoid poor wire feeding.
11.Use both hands to steady the gun when you weld. Do this whenever possible. (This also applies to Stick and TIG welding, and plasma cutting.)
12. Keep wire feeder hub tension and drive roll pressure just tight enough to feed wire, but don¹t overtighten.
13. Keep wire in a clean, dry place when not welding, to avoid picking up contaminants that lead to poor welds.
14. Use DCEP (reverse polarity) on the power source.
15. A drag or pull gun technique will give you a bit more penetration and a narrower bead. A push gun technique will give you a bit less penetration, and a wider bead.