An introduction to TIG welding
- Share
- Issue Time
- Dec 27,2019
Summary
Of all the arc welding processes, TIG (tungsten inert gas) welding is capable of achieving the highest quality welds and is the most versatile in terms of what can be welded and the position of the welds. As in most industrial processes, however, quality comes at the expense of time and TIG is generally slower than MIG or MMA welding. But, where weld integrity is critical, production engineers are prepared to accept the additional process time.
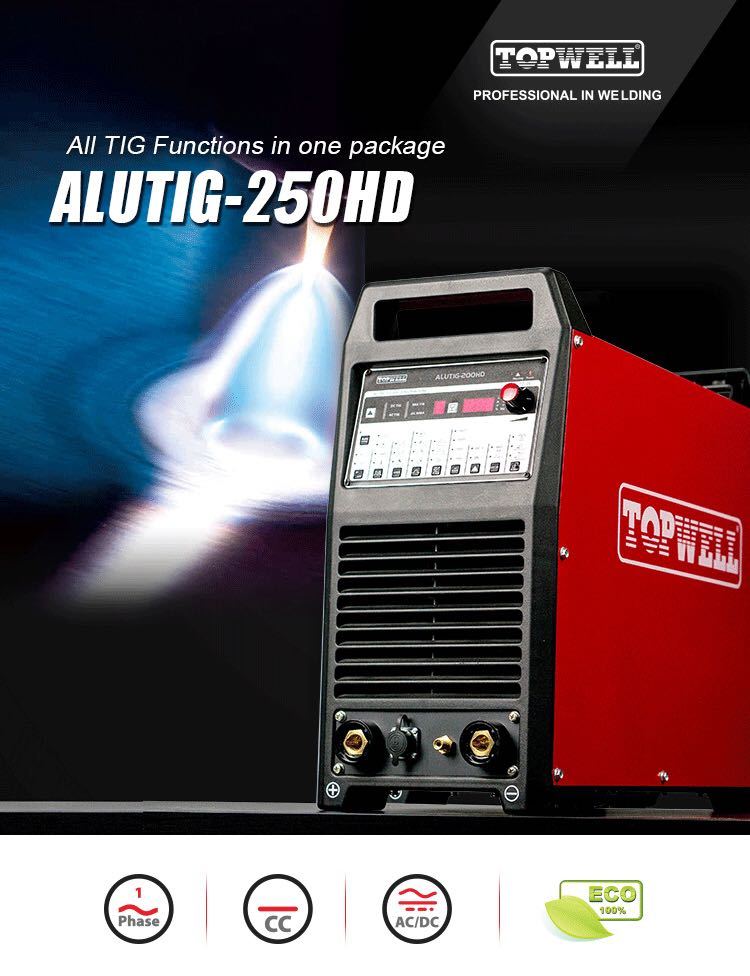
An introduction to TIG welding
Of all the arc welding processes, TIG (tungsten inert gas) welding is capable of achieving the highest quality welds and is the most versatile in terms of what can be welded and the position of the welds. As in most industrial processes, however, quality comes at the expense of time and TIG is generally slower than MIG or MMA welding. But, where weld integrity is critical, production engineers are prepared to accept the additional process time.
TIG welding is an extremely versatile process; it can be used with virtually any weldable metals, including dissimilar metals, and thicknesses from 0.5mm upwards. TIG welding machines are typically available in current ratings from 150A to 350A and they are capable of operating at currents as low as, typically, 3A for a 150A machine. In addition, TIG machines can be used for brazing and MMA welding, which helps to improve the return on an investment in TIG equipment.
The most commonly used shielding gas for TIG welding is pure argon for all materials including aluminium. For thick aluminium and copper, argon/helium would be used for the added heat from the helium. TIG operatives do need to be aware that the correct tungsten electrode must be used, otherwise problems can be experienced with striking the arc and maintaining a stable arc.
Excellent finish
One of the advantages of TIG welding is that the weld not only possesses high integrity but it also has a very aesthetic surface finish. Consequently welds can often be left 'as is', with no need for grinding. This is beneficial in terms of the time saved, plus it avoids any problems associated with grinding on site, such as noise, vibration and dust. Depending on the model of TIG welder used, the operative can have control over many of the weld parameters so as to optimise the weld quality. Modern inverter-based TIG power sources are lighter and more portable than traditional units, so on-site TIG welding is commonplace for both fabrication and modifications/repairs.
Typical applications for TIG welding include:
· architectural stainless steel fabrications, such as balustrades
· vessels and pipework for the offshore, petrochemical and nuclear industries
· aluminium alloy, magnesium and titanium fabrications for the aerospace industry, where weld integrity is paramount
· motorcycle and bicycle frames, where TIG-welded joints offer both high integrity and a good surface finish on joints that will still be visible after final assembly
· stainless steel pipework, vessels and machine frameworks for the food, beverage and dairy industries
More unusual applications include jewellery (even gold can be welded with TIG), dentistry (for chrome cobalt frameworks) and titanium (for specialist high-strength, low-weight applications). For fine work and low-current applications, TIG is increasingly being used as a more versatile alternative to micro-plasma welding.