PROWAVE a technical platform of Advanced process welder fronius replacement
- Model
- PROWAVE
Review
Description
DETAILS
PROWAVE SERIES
SMAW
GMAW
FCAW
GTAW-Lift Arc
CAC-A
PROWAVE Versions
Capacity
|
350C |
500i
|
650i
|
Cooling variants
|
|||
Gas
|
● |
○
|
○
|
Water |
○ |
●
|
●
|
Wire feeder system | |||
Built-in wire feeder system | ● | ○ | ○ |
Separately wire feeder system | ○ | ● | ● |
Operation method | |||
At the main power source | ● | ● | ● |
At the Wire feeder | ○ | ● | ● |
At the remote control | ○ | ○ | ○ |
At the torch | ○ | ○ | ○ |
● Standard ○Optional
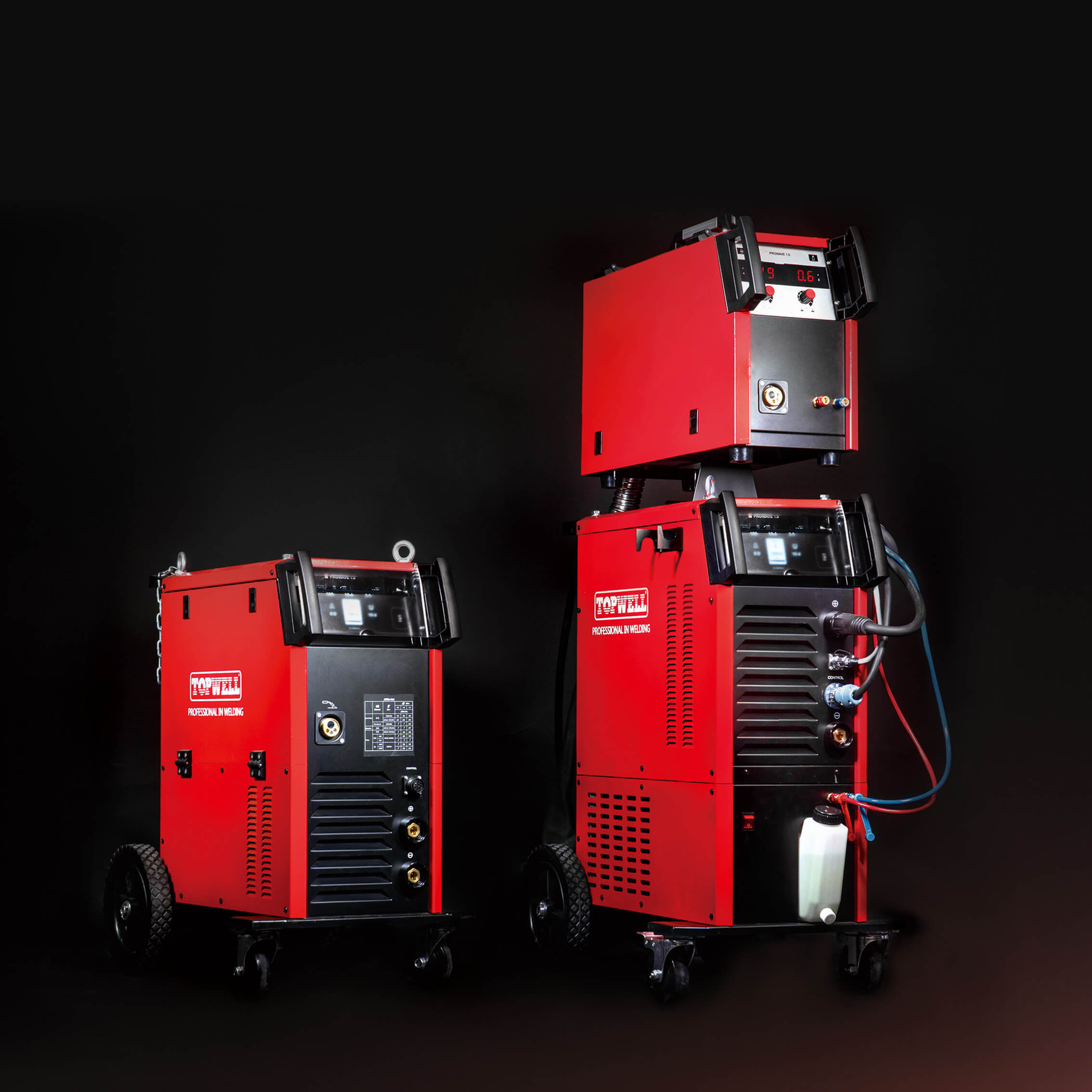
Friendly I/O interface
At standby page:
Direct to the main parameters and fix the setting quickly.
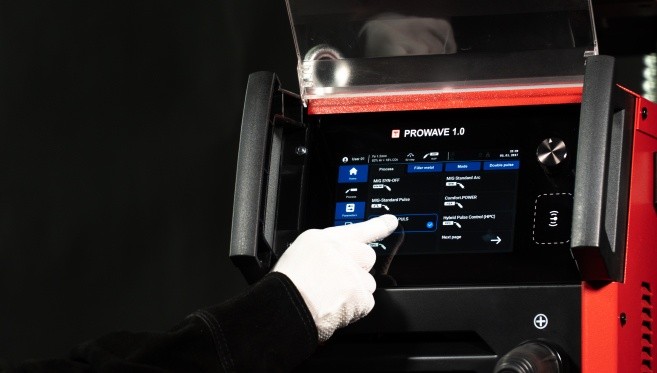
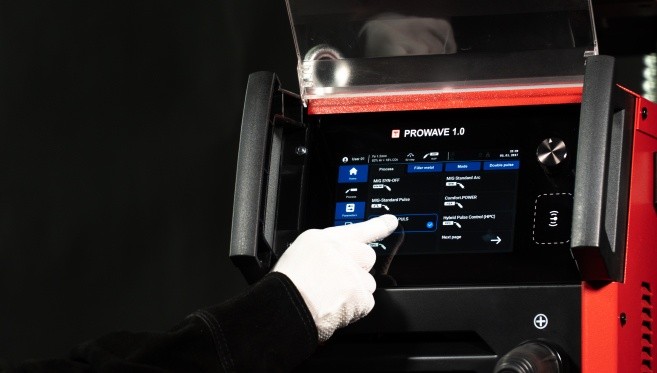
Simply undestand the operation logics even new to this system
Flexibility: you can regulate the machine everywhere ----- at the power source, at ....
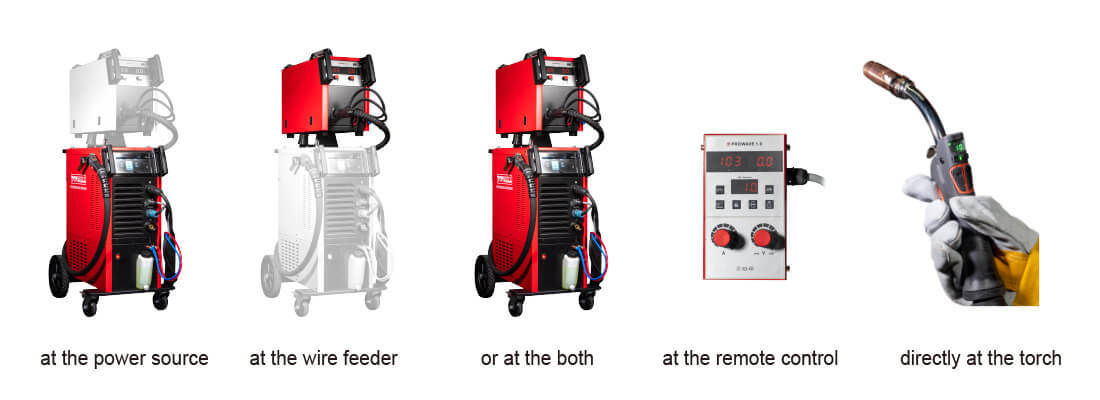
Remote control
• Can Set and display all welding parameters, suitable for long-distance welding work and non-fixed workstation.
• Robust metal casing with mounting bracket / Plastic cover.
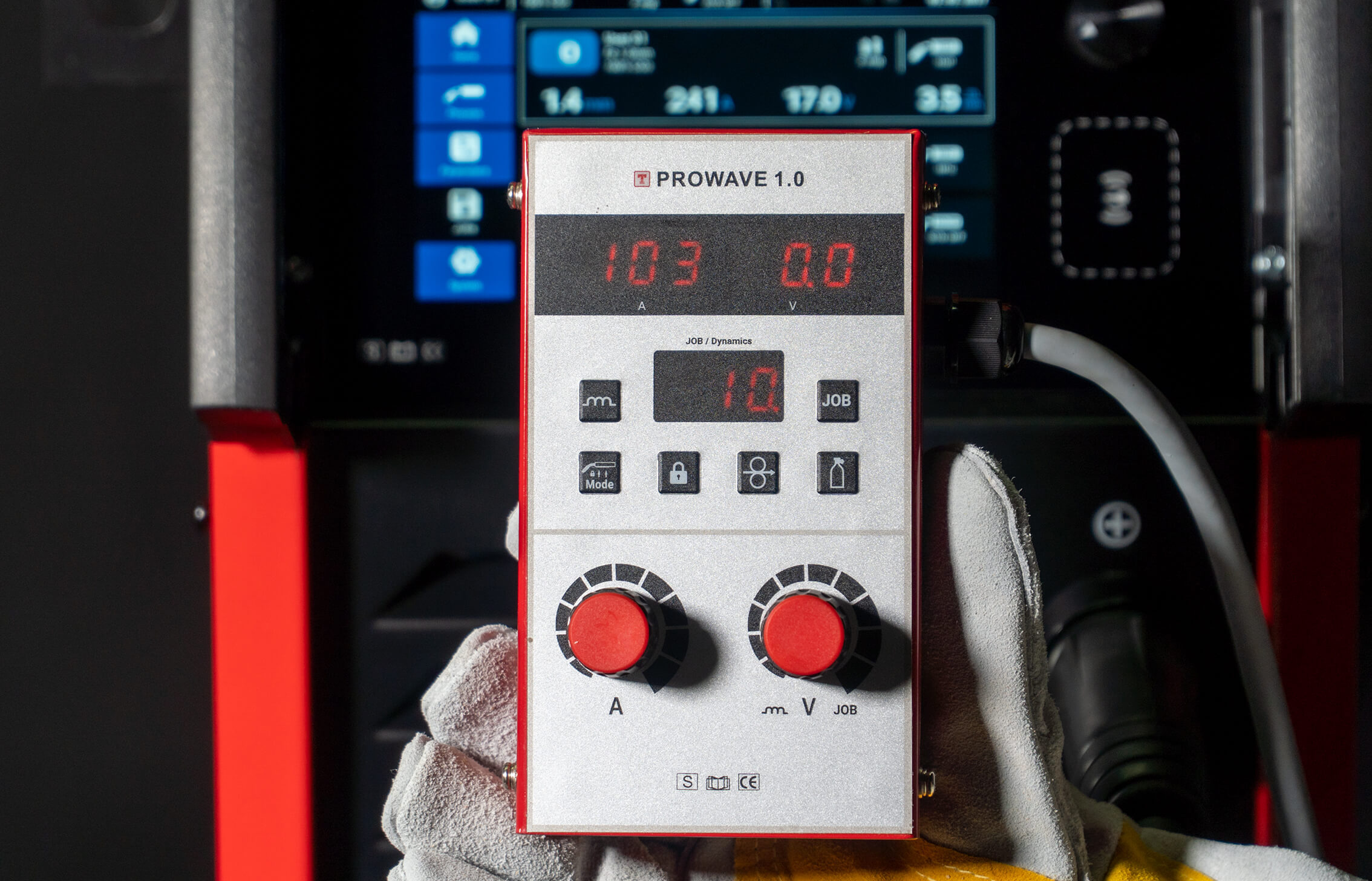
Digital welding torch
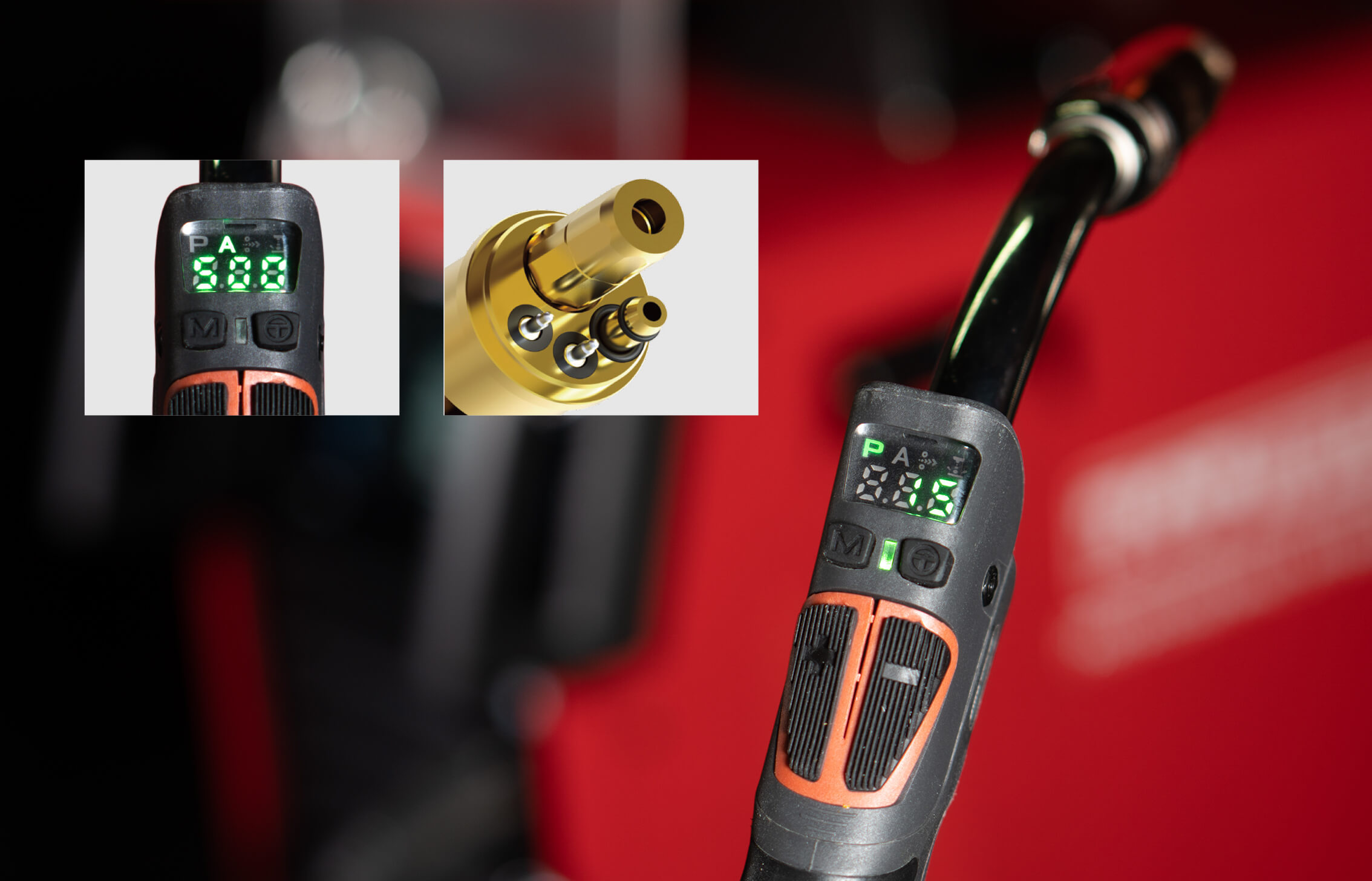
Various welding parameters can be quickly adjusted with the torch without moving back,
save more time and improve working efficiency.
Long distancewelding work
Ultra-Long cable loop compensation function
Intelligent compensation makes welding more stable, especially suitable for oversized workpiece welding occasions.
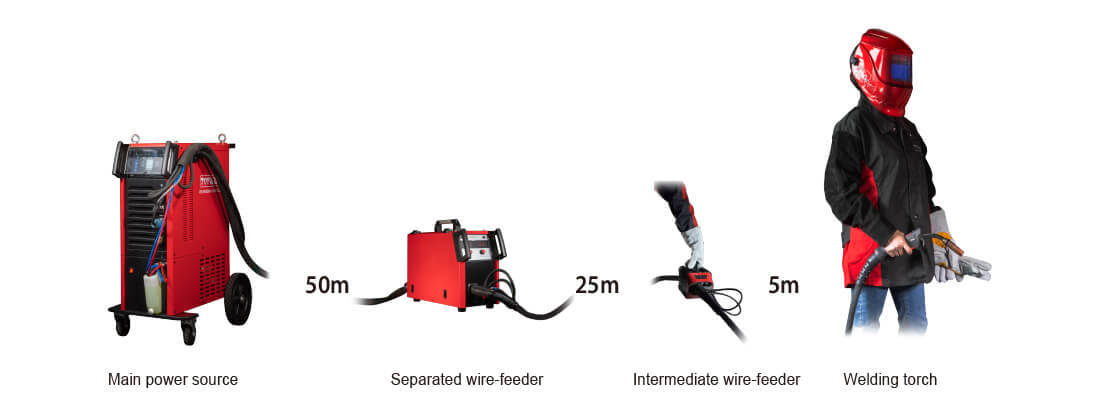
Multi processes
PROWAVE integrates a variety of welding processes, covering MIG, TIG, MMA, and Gouge. Welders can easily select and switch welding processes through the LCD screen, and use different welding processes to weld multiple metals. There is no need to purchase separate equipment for each type of welding process, to meet the challenges of large-scale industrial manufacturing projects.
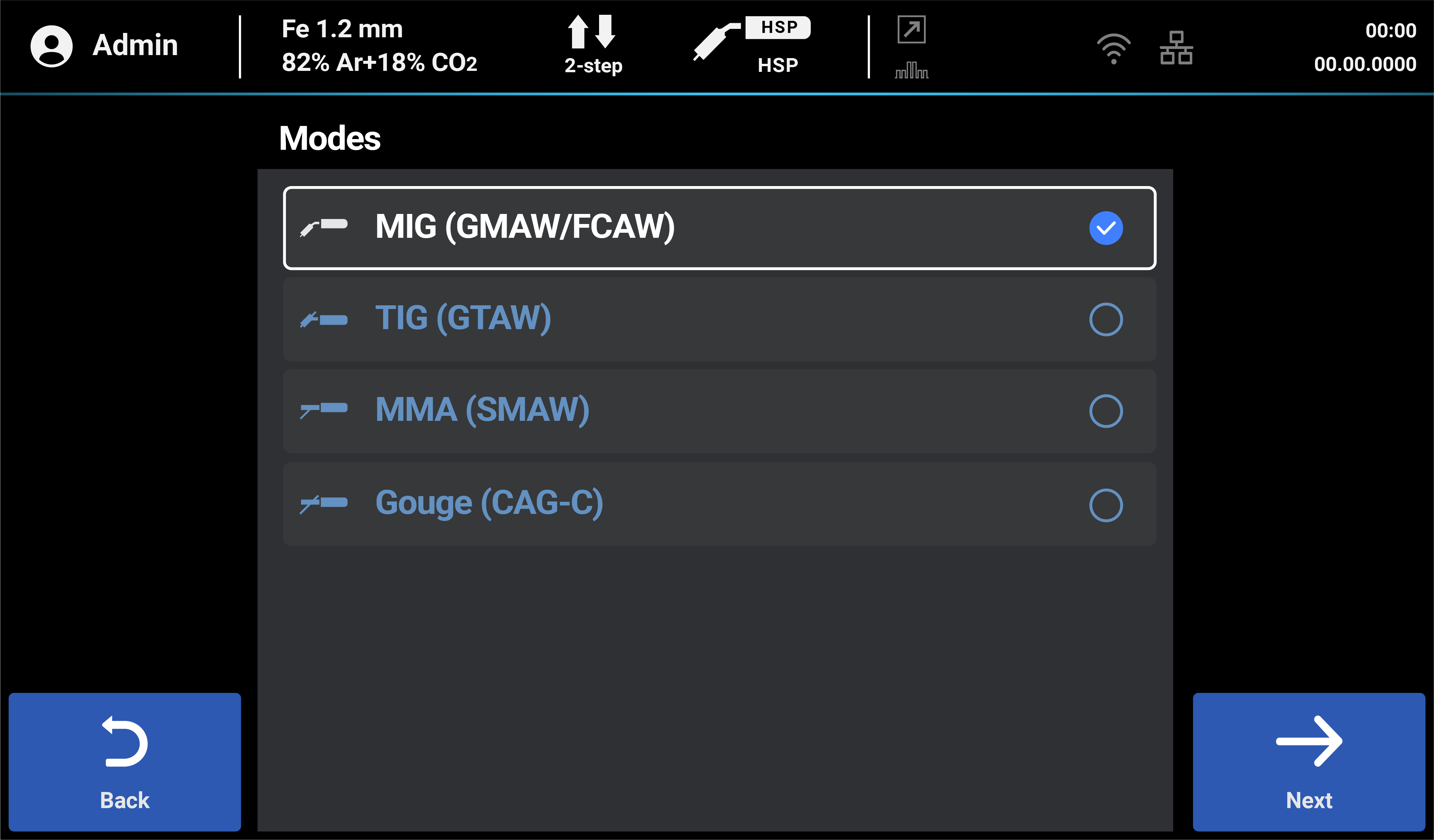
Multiple robot communication methods
Flexible selection of multiple communication methods, achieve seamless integration with different brands of robots.
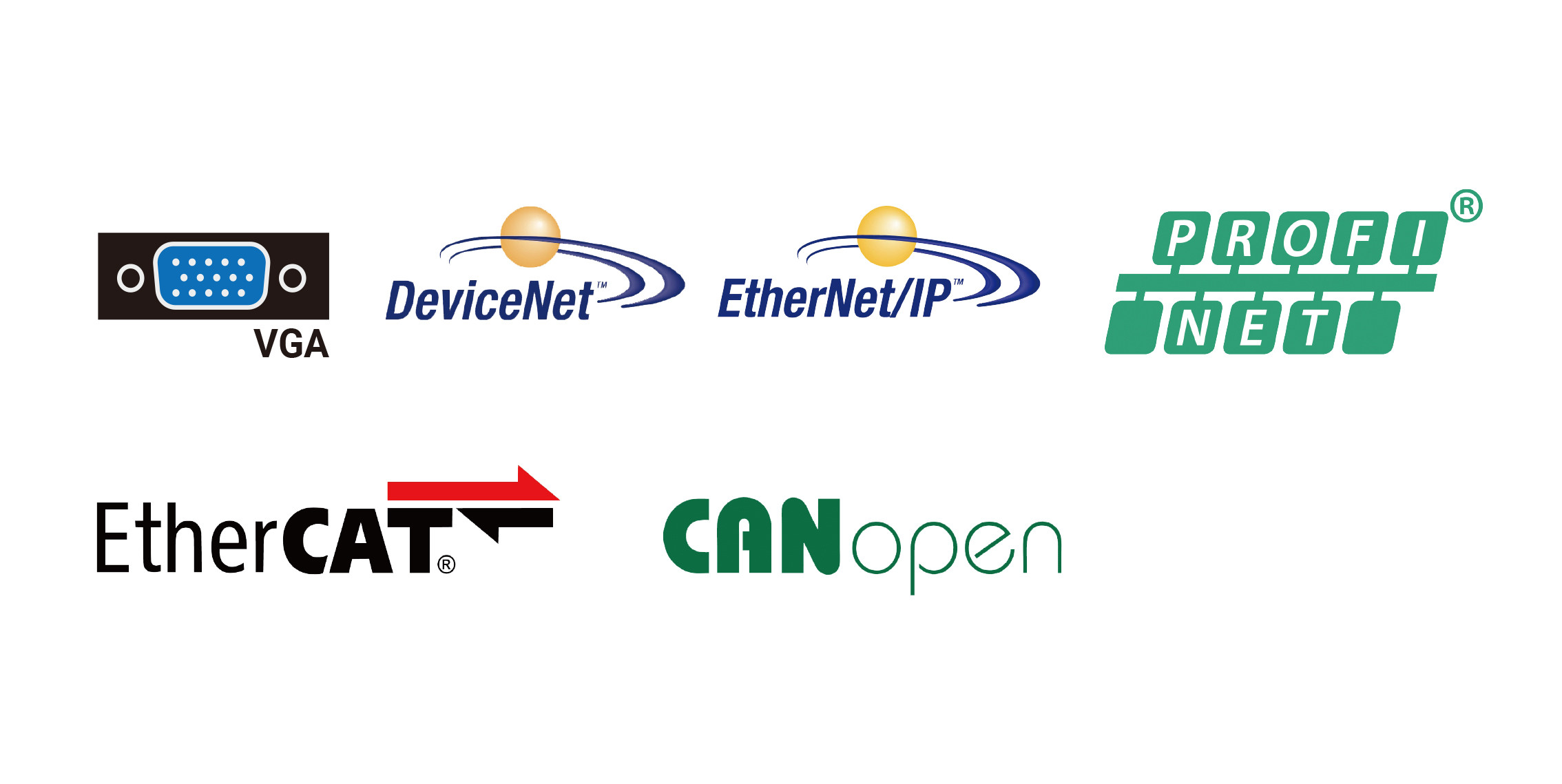
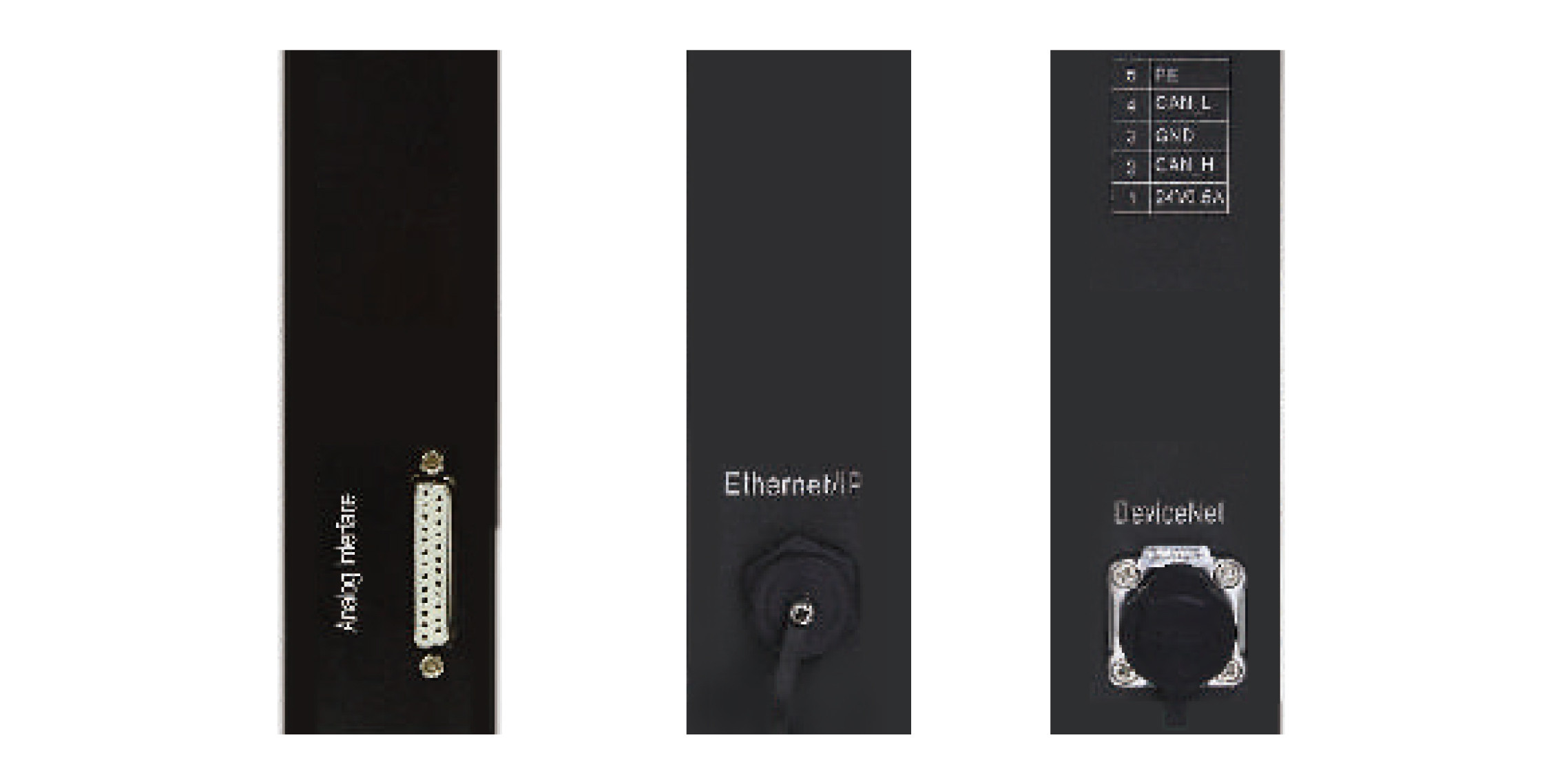
Robot communication modes
|
|||||
Analog
|
Enternetlp
|
DeviceNet | CAN |
CANOPEN
|
RJ485
|
●
|
○
|
○ | ○ |
○
|
○
|
● Standard options ○ Optionally available
Optional remote control box design
Ultra-Long cable loop compensation function
Full digital communication interface, achieve seamless integration with different brands of robots, also available for MES system.

Data exchange & storage via USB
Welding tasks & data can quickly exchange via a USB flash memory, it can update the main control system and restore the default setting parameters easily.

HSP - High Speed Pulse
-Specifically designed for demanding workshop use,the deposition rate can increase 25~48 % for various materials, whether used in manufacturing thick materials or sheet metal.
-The High-Speed Pulse(HSP) process enables you to save time, money, and energy compared to traditional pulse welding. This process is ready to raise pulse welding to a whole new level!
-In general, One pulse melt one droplet, but we increase the submission of these droplets by TOPWELL’ s New High-Speed pulse process.The transition will be faster, narrower HAZ zone and deeper penetration!
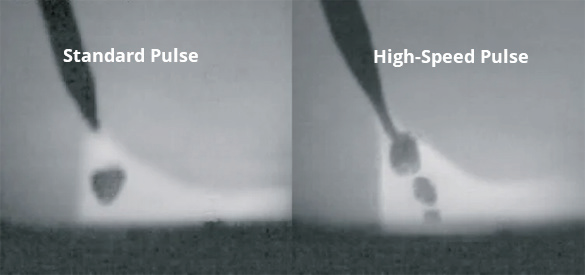
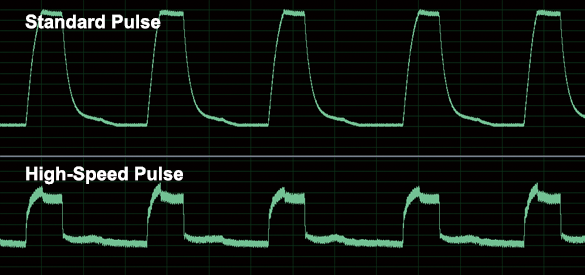
Get better welding seam
Less heat input, less spatters, less rework.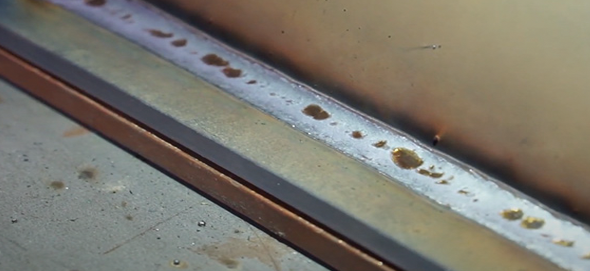
Get higher welding strength
Deeper penetration, no undercut defects, higher strength.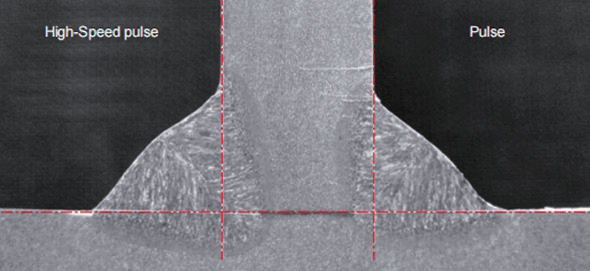
HPC - Hybrid Pulse Control
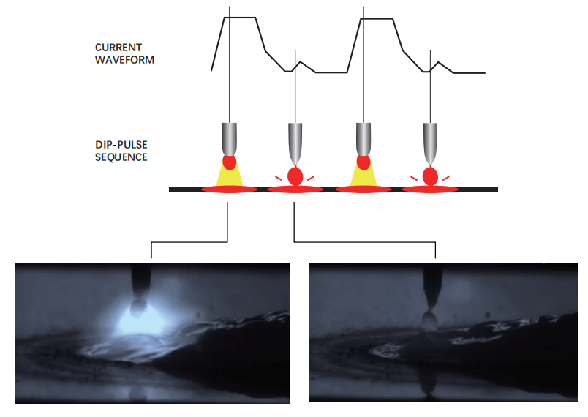
The key is synergetic waveform controlled welding process control variants applied in MIG welding which are Pulse(spray arc) and short-circuit transfer types in one duty cycle. It delivers exceptional directional stability, deep penetration and free-spatters.
HPC Vertical-up Welding Process
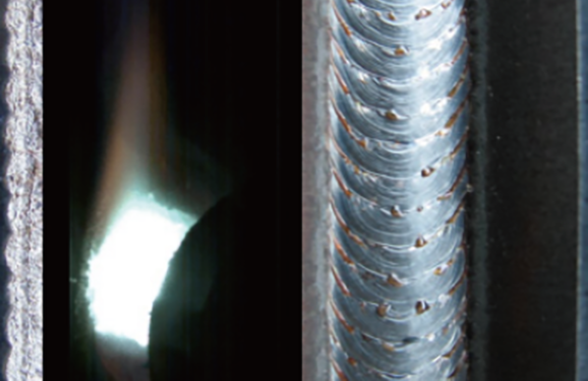
HDP - High-speed Double Pulse
HDP is the High-Speed Double Pulse. The high and low pulse phases of the double pulse work with the High Speed Pulse process, the deposition rate is increased by up to 30%, the welding productivity is significantly improved than a standard double pulse. The professional welding curve for excellent control of heating and cooling phases, ensures precise energy input, low spatter, low distortion and a beautiful TIG-like welding appearance. HDP is particularly suitable for medium to thick-walled welding, especially for Aluminum and Steel applications.
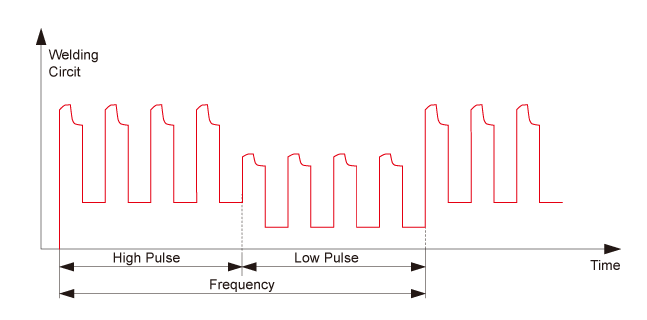
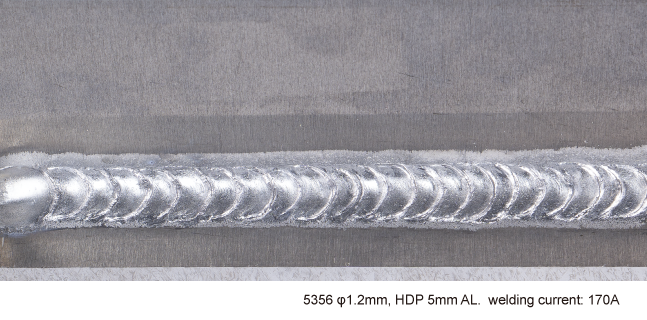
HSA - High Speed Spray Arc
The perfect combination of a highly concentrated and extremely stable arc with high density. HSA delivers deeper penetration, narrower heating zone, allows smaller opening angles for multi-layer welding, significantly improves the welding speed up to 30% faster than conventional MIG-MAG welding. It makes welding more efficient and more economical.

Smaller opening angle
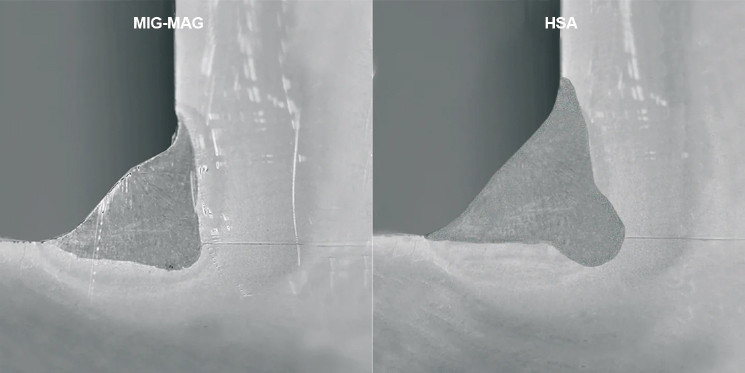
Deeper penetration
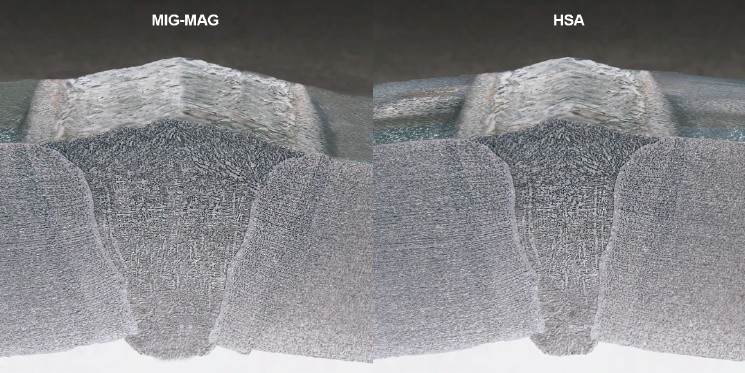
More material saving
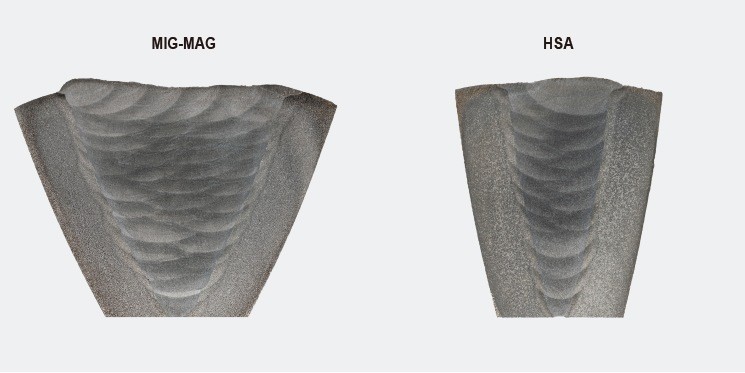
Higher welding efficiency
MDP - Micro Double Process
MDP is Micro Double Process, ultra-precise on the synergy Pulse wave-form controlled process-control, freely adjust the weld seam chevrons from coarse to fine. The key is that when the high and low pulses alternate, there is no droplet formation in the low pulse phase. The advantage of MDP are precise energy input, low distortion, perfect TIG-like welding appearance easily produced by anyone, and the welding productivity can up to twice as quick as the conventional TIG. MDP is particularly suitable for thin to medium-walled (1-8mm) Aluminum, Steel, and CrNi applications, like frames, tables, beds, and furniture structures.
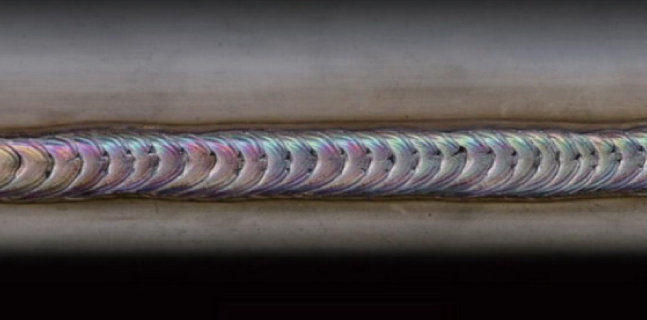
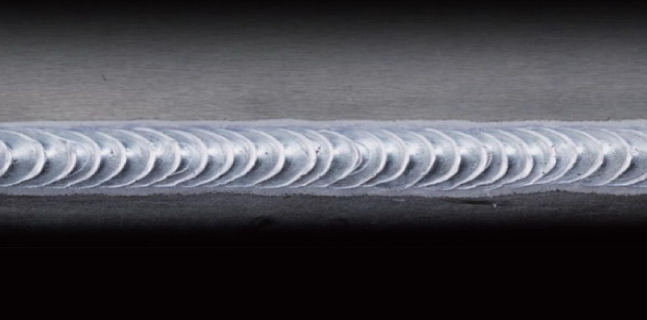
ULS - Ultra Low Spatters
The ULS process is a modified short-arc transfer arc, it controls the volatility during the change of state between short and arc to control the amount and size of the spatter generated. Even in CO2 and MAG welding, it can minimize the spatters, which means less rework, fewer rejects, less cleaning required and savings on wearing parts.
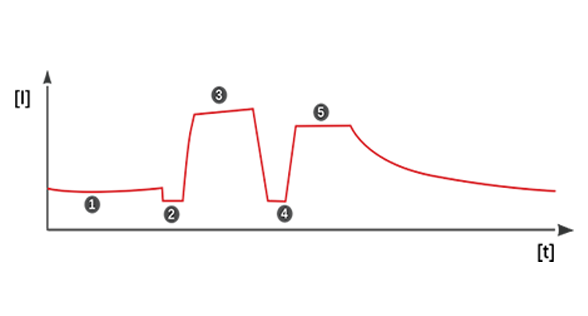
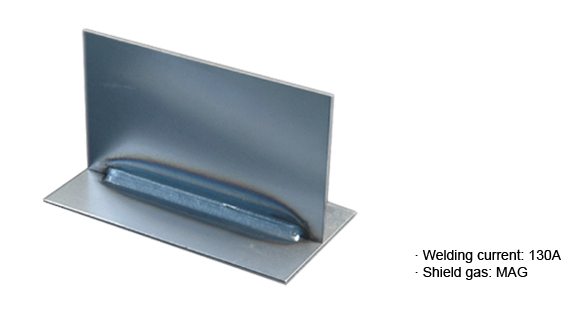

HSS - High Speed Spot Technology
HSS is the high speed spot welding, which is perfectly combining the welding process, arc physics, high dynamic power response and powerful motor control technology, short in arc ignition time and arc ending time, a welding spool can be formed swiftly. A spot welding cycle is quickly completed, cycle over and over, by adjusting the time gap with the robot to get the fish scale you wish, weld seam is clear and beautiful.
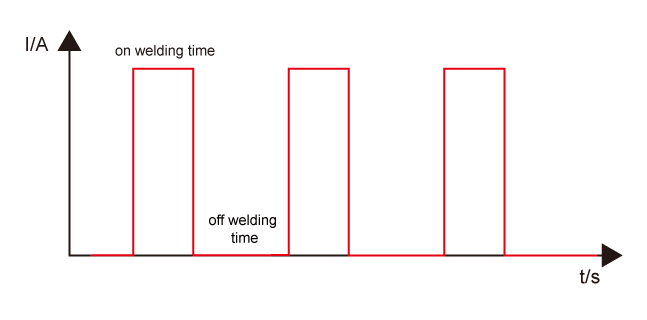
Tack welding: by robot
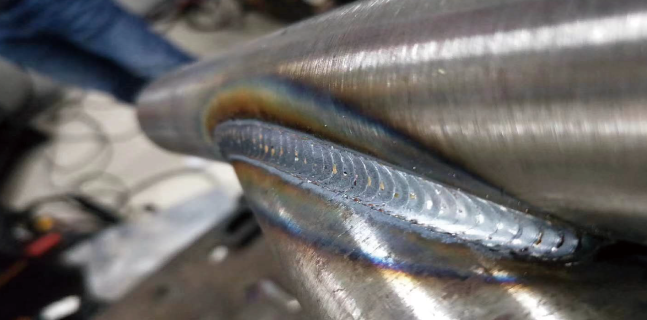
Widely applied on the thin (≤2mm thickness) pipes or frame/structure welding jobs.
Improved Operation Process & Controls
Arc Length control
With the arc length control, no matter the changing distance between the torch and the workpiece, or the welding voltage, the arc length is kept constant, and the seam quality and appearance remain unchanged.
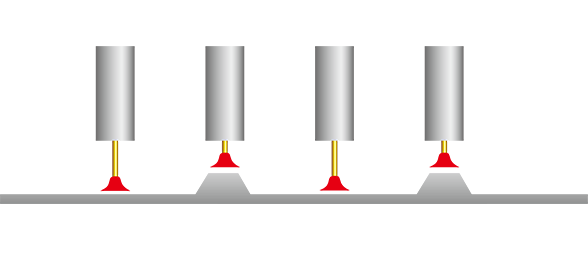
Dynamic control
The arc can easily be adjusted depending on the workpiece and positions as well as to the individual preferences of the welder through Dynamic Control. Changing the arc to soft or hard or anywhere in between, increases the reliability for a good root formation and side fusion even with a non-ideal position of the torch.
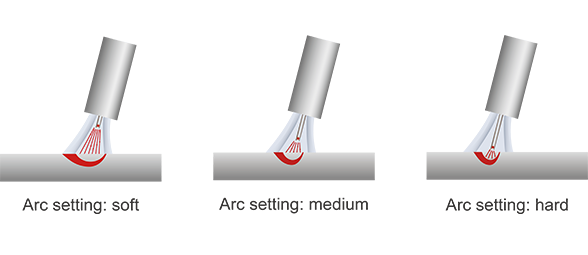
Initial Arc control & Burn Back control
Initial Arc control is used to improve the success rate of arc ignition and form a smaller molten ball. Burn Back Control enhances the function of eliminating molten ball, making the secondary arc initial easier.
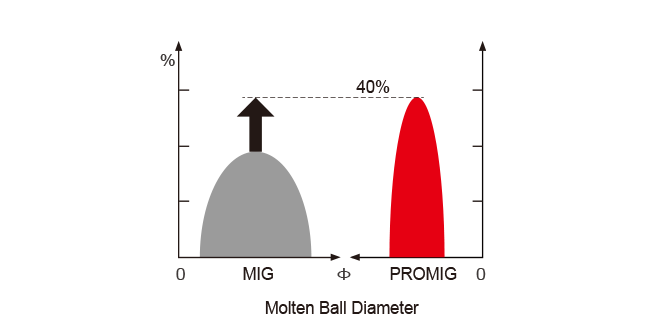
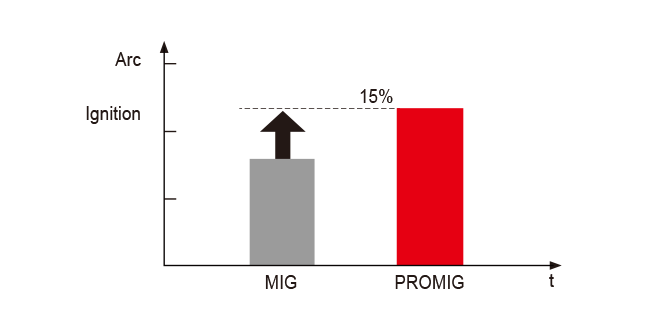
Application
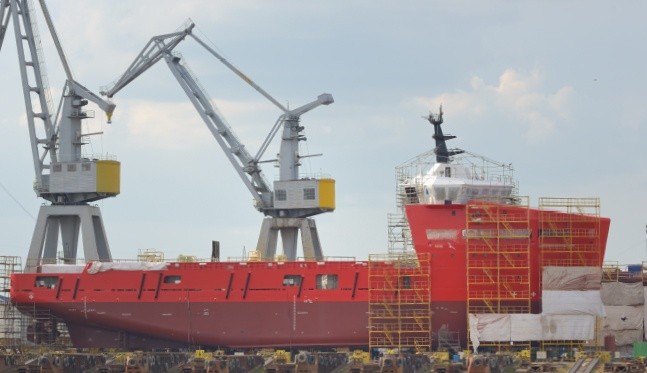

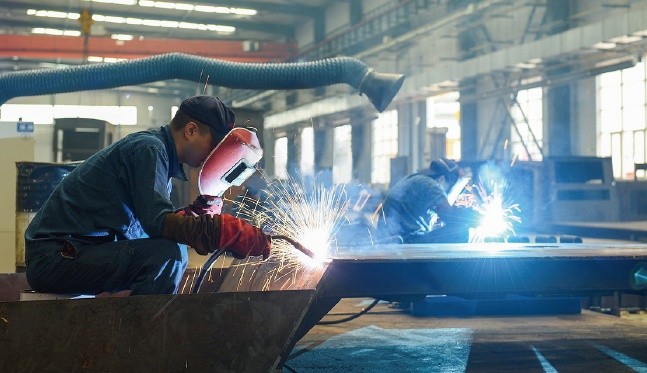
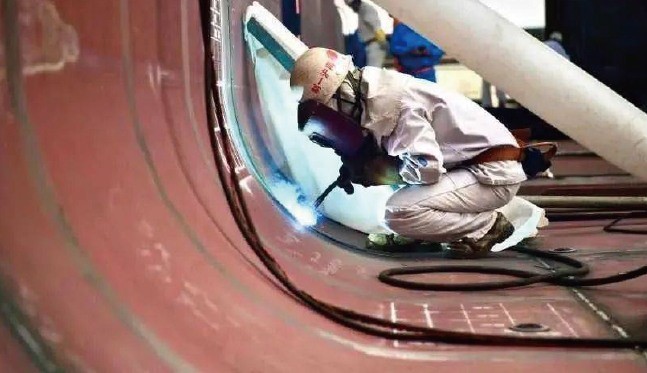
VIDEO
SPECIFICATIONS
Product Name
|
PROWAVE-350C | PROWAVE-500i |
PROWAVE-650i
|
Mains voltage(V) |
3PH~400V±15%(50/60Hz) | 3PH~400V±15%(50/60Hz) |
3PH~400V±15%(50/60Hz) |
Max.Load Power Capacity |
18.1KVA | 25.83KVA |
30.1KVA
|
Output Range | MIG: 30A/15.5V~350A/31.5V | MIG: 30A/15.5V~500A/39V | MIG: 30A/15.5V~650A/44V |
Rated Duty cycle at 40℃ (105℉): 60% | MIG: 350A/31.5V | MIG: 500A/39V | MIG: 650A/44V |
100% | MIG: 250A/26.5V | MIG: 400A/31.5V | MIG: 500A/39V |
Open Circuit Voltage | 70V~80V | 70V~80V | 70V~80V |
Power Factor | 0.87 | 0.87 | 0.87 |
Efficiency | 89% | 89% | 89% |
Wire feed unit | 4 rollers | 4 rollers | 4 rollers |
Wire feed speed range | 0~25m/min | 0~25m/min | 0~25m/min |
Wire SpoolCapacity | 300mm(15~20kg) | 300mm(15~20kg) | 300mm(15~20kg) |
Wires φ (mm): Fe | 0.8~1.2mm | 0.8~1.6mm | 0.8~1.6mm |
Alu | 1.0~1.2mm | 1.0~1.2mm | 1.0~1.2mm |
Flux-cored | 1.0~1.2mm | 1.0~1.6mm | 1.0~2.0mm |
Dimension (L x W x H): Machine | 760 x 300 x 780mm | 760 x 300 x 880 mm | 760 x 300 x 1030 mm |
Wire feeder | / | 650 x 250 x 460 mm | 650 x 250 x 460 mm |
Net Weight : Machine | 63kg | 66.5kg | 76kg |
Wire feeder | / | 15kg | 15kg |
YOU MAY ALSO NEED